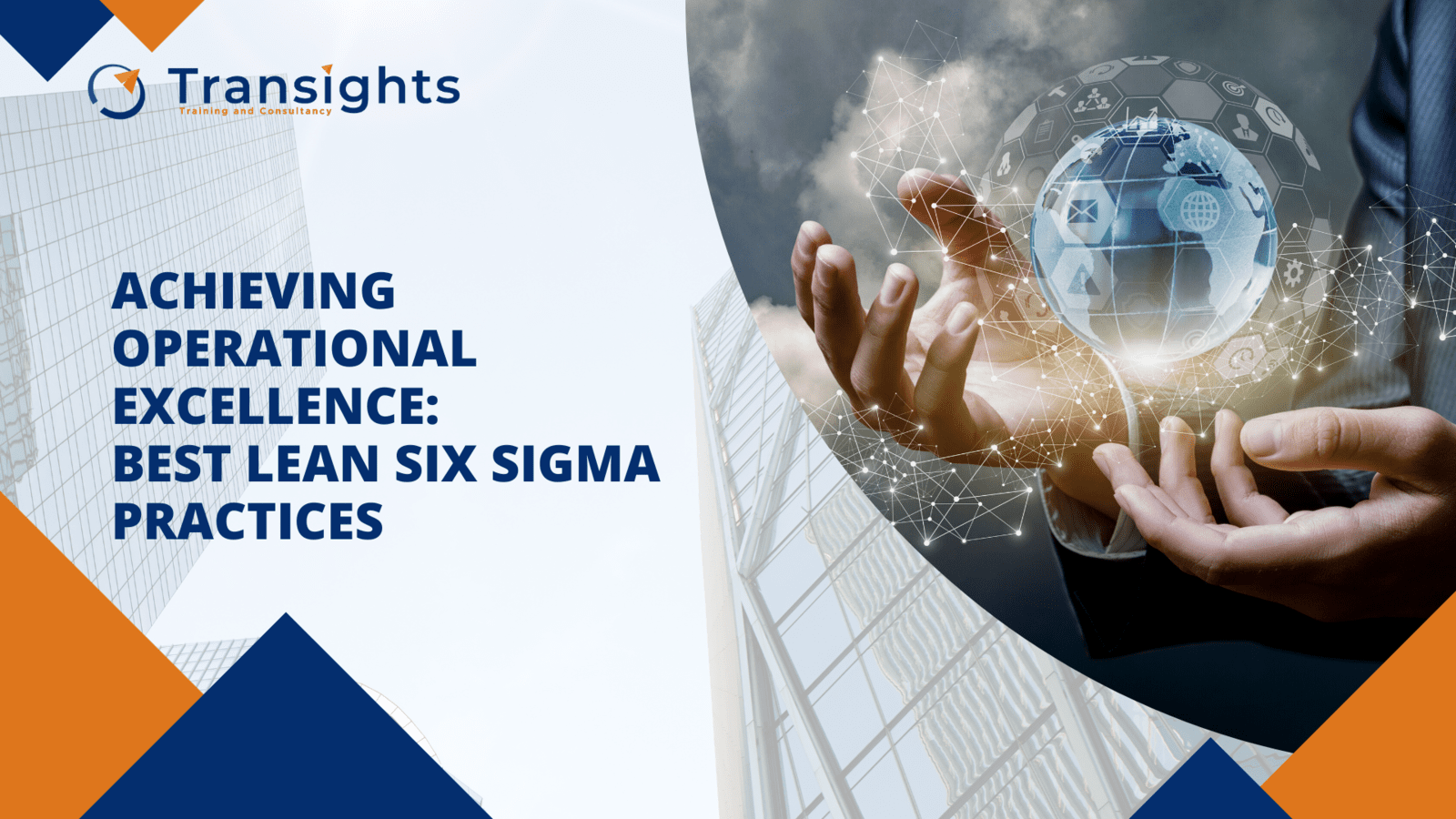
Lean Six Sigma, a powerful methodology that combines Lean manufacturing principles and Six Sigma techniques, has become a cornerstone for organizations aiming to enhance operational efficiency, reduce waste, and improve overall quality. By integrating these practices, businesses can streamline processes, boost productivity, and deliver higher value to customers. In this article, we explore the best Lean Six Sigma practices that organizations can adopt to achieve operational excellence.
Define and Align with Customer Value:
Define and Align with Customer Value:
The foundation of Lean Six Sigma lies in understanding and meeting customer requirements. Clearly defining the value stream and ensuring that every process contributes to delivering value to the customer is essential.
Continuous Improvement Culture:
Continuous Improvement Culture:
Foster a culture of continuous improvement within the organization. Encourage employees at all levels to identify opportunities for improvement, share ideas, and actively participate in problem-solving initiatives.
DMAIC Methodology:
DMAIC Methodology:
Utilize the DMAIC (Define, Measure, Analyze, Improve, Control) framework for process improvement. This structured approach provides a systematic way to identify and address issues, ensuring sustained improvement over time.
Data-Driven Decision-Making:
Data-Driven Decision-Making:
Base decisions on data and facts rather than assumptions. Collect and analyze relevant data to gain insights into process performance, identify root causes of issues, and measure the impact of improvement initiatives.
Cross-Functional Teams:
Cross-Functional Teams:
Form cross-functional teams that bring together individuals with diverse skills and perspectives. Collaboration across departments ensures a comprehensive understanding of processes and facilitates holistic problem-solving.
Standardization of Processes:
Standardization of Processes:
Standardize processes to reduce variability and enhance predictability. Clearly documented and standardized procedures contribute to consistency and make it easier to identify deviations and areas for improvement.
Kaizen Events:
Kaizen Events:
Implement Kaizen events, which are focused, short-duration improvement activities. These events bring together teams to address specific issues or make targeted improvements, often resulting in quick wins and sustained progress.
Visual Management:
Visual Management:
Utilize visual management tools, such as Kanban boards and process maps, to enhance communication and transparency. Visualizing processes makes it easier to identify bottlenecks, monitor progress, and engage teams in improvement efforts.
Training and Skill Development:
Training and Skill Development:
Invest in training programs to develop Lean Six Sigma skills across the organization. Ensuring that employees have the necessary knowledge and tools empowers them to actively contribute to improvement initiatives.
Leadership Engagement and Support:
Leadership Engagement and Support:
Leadership support is crucial for the success of Lean Six Sigma initiatives. Engage leaders at all levels, communicate the importance of continuous improvement, and ensure that resources are allocated to support improvement projects.
Conclusion:
Conclusion:
Lean Six Sigma provides a structured and data-driven approach to achieving operational excellence. By adopting these best practices, organizations can build a culture of continuous improvement, enhance collaboration, and drive measurable and sustainable results. As businesses navigate the complexities of today's competitive landscape, Lean Six Sigma stands as a valuable methodology for organizations striving to deliver exceptional quality and value to their customers.