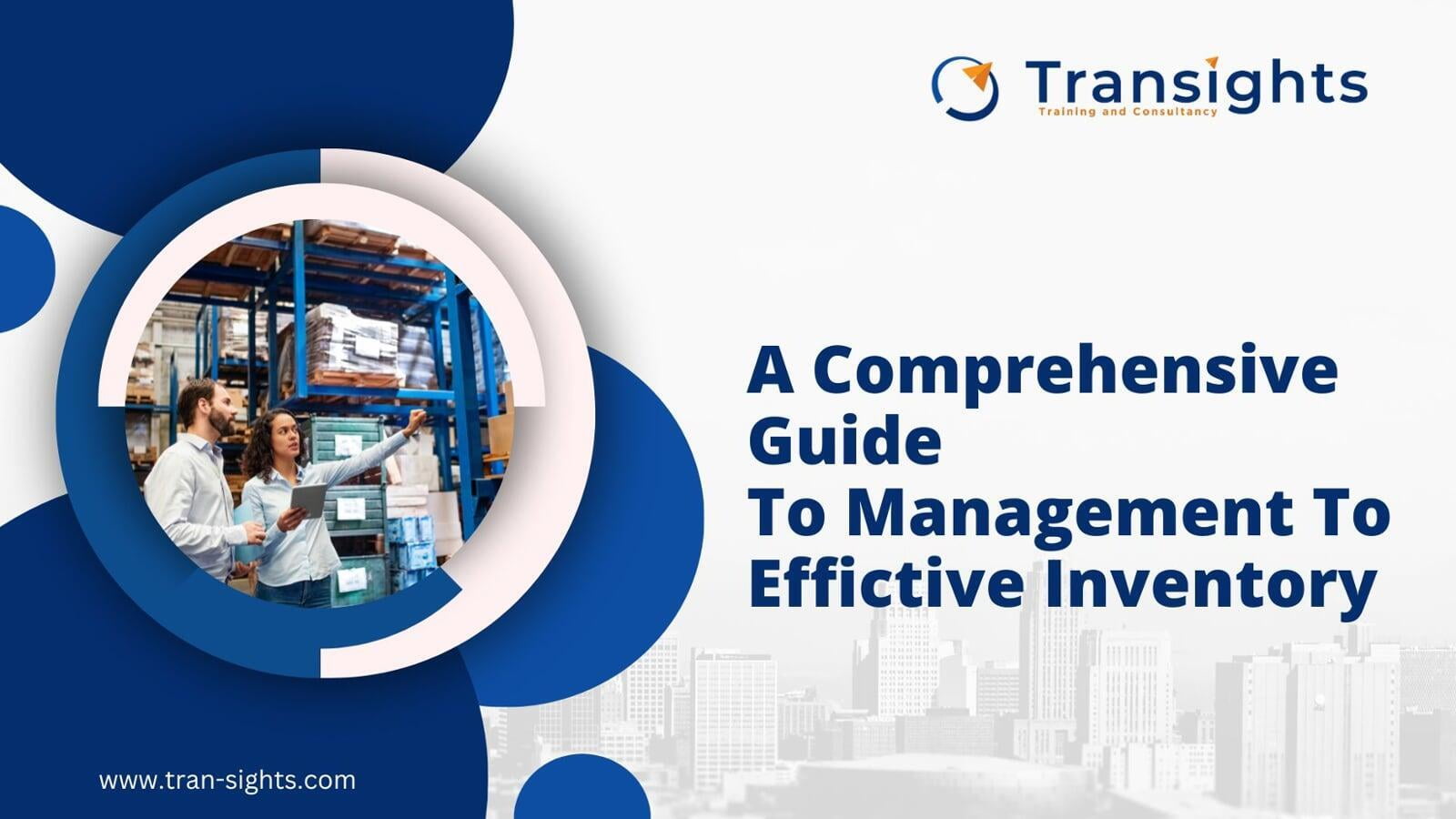
Inventory management plays a pivotal role in the success of any business, regardless of its size or industry. Efficiently managing stock not only ensures smooth operations but also contributes significantly to customer satisfaction and financial stability. This article explores the key aspects of inventory management, providing insights into its importance, challenges, and best practices.
Importance of Inventory Management:
Optimizing Cash Flow:
- Efficient inventory management prevents overstocking and understocking, ensuring that capital is not tied up unnecessarily in excess inventory.
- Balancing stock levels helps maintain a healthy cash flow, allowing businesses to allocate resources to other critical areas such as marketing, research, and development.
Meeting Customer Demand:
- Timely and accurate inventory tracking enables businesses to meet customer demands promptly.
- By having the right products in stock, companies can enhance customer satisfaction and loyalty, leading to repeat business and positive word-of-mouth.
Reducing Holding Costs:
- Storing excess inventory incurs additional holding costs such as warehouse space, insurance, and security.
- Effective inventory management minimizes holding costs by maintaining optimal stock levels, freeing up resources for other strategic investments.
Challenges in Inventory Management:
Demand Forecasting:
- Inaccurate demand forecasting can lead to overstocking or stock outs, Advanced analytics and historical data analysis can improve forecasting accuracy.
Supply Chain Disruptions:
- External factors like natural disasters, political unrest, or global pandemics can disrupt the supply chain, affecting inventory levels.
- Building resilient supply chains with backup suppliers and inventory buffers helps mitigate the impact of such disruptions.
Technological Integration:
- Some businesses still rely on outdated manual systems, leading to errors, delays, and inefficiencies.
- Adopting advanced technologies such as inventory management software and RFID systems can streamline processes and enhance accuracy.
Best Practices in Inventory Management:
Regular Audits and Cycle Counts:
- Conducting regular audits and cycle counts helps identify discrepancies between actual and recorded inventory levels.
- This proactive approach minimizes the risk of errors and ensures data accuracy.
ABC Analysis:
- Categorizing inventory into A, B, and C categories based on importance helps prioritize management efforts.
- High-value items (A category) require closer monitoring and strategic decision-making compared to lower-value items (C category).
Just-in-Time (JIT) Inventory System:
- JIT systems aim to minimize inventory levels by receiving goods only as they are needed in the production process.
- This approach reduces holding costs and increases efficiency but requires a reliable and responsive supply chain.
Collaboration with Suppliers:
- Establishing strong relationships with suppliers helps in negotiating favorable terms, ensuring timely deliveries, and maintaining consistent product quality.
- Collaborative partnerships contribute to a more responsive and agile supply chain.
Conclusion:
Effective inventory management is a cornerstone of operational success, impacting a business's financial health, customer satisfaction, and overall competitiveness. By embracing best practices and leveraging technology, organizations can navigate the challenges and optimize their inventory processes. A well-managed inventory not only meets current demands but also positions a business for growth and resilience in the dynamic marketplace.